A Guide to Proper Storage and Inventory Management in Your Commercial Facility
- Admin
- Sep 28, 2022
- 11 min read
Updated: Oct 6, 2022

Every business, especially those dealing with large amounts of stock and supplies, needs an efficient storage and inventory management system. However, many businesses lack the necessary equipment and knowledge to keep their storage facilities organised and safe for their employees, customers, and for smooth operations. Whatever industry you’re in, here’s a guide to help you ensure an efficient storage system for your company.
Proper Storage and Inventory Management
1.1. What is Inventory Management?
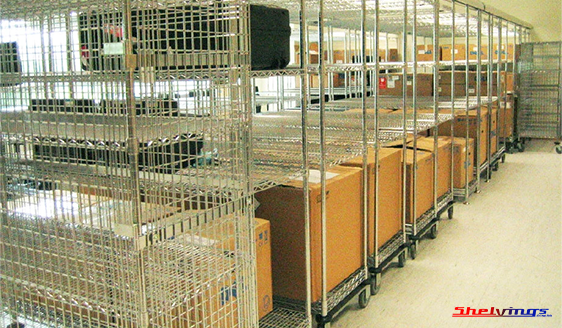
Inventory management tracks supplies in your warehouse throughout its life cycle. From procurement to sales, proper stock management assists in determining which item and quantity to order at each stage of your operations. This practise ensures that there are always sufficient goods to fulfil customer orders.
1.2. Why is Inventory Management and Efficient Storage Important?
Businesses should prioritise an efficient storage system and proper inventory control. Because when a company has control over its stock, there will be improvements in warehouse efficiency, better customer service and a clearer view of profit margins. Businesses that are not in the manufacturing and sales industries also need proper storage to organise their supplies and ensure efficient operations by keeping things neat and easy to find. The main benefits of inventory management and a clean storeroom are as follows:
Lower Costs and Improve Cash Flow

Having better visibility of your inventory allows you to keep track of what you have and what you don’t, and reduces the risk of you ordering too much of an item that you already have in stock. Costs such as freight, shipping, and handling are reduced to save money and improve your business’s cash flow.
Maximise Use of Space
Ensuring an adequate supply of goods and not stockpiling with excess items keeps the storage facility clean and tidy, making room for other purposes and increasing efficiency of your space, such as being able to utilise the area for revenue generation.
Improve Work Process
An organised space keeps things visible and allows employees to spot items they need at a glance. You’ll be wasting less time looking for stock, and more time doing productive tasks.
1.3. Storage Tips for Commercial Facilities
Select Climate-Controlled Storage Units

A climate-controlled facility promotes air circulation to keep dust and other particles at bay, as well as low humidity levels to prevent moisture and mould build up, all of which can lead to equipment deterioration or damage to your goods. Climate control is essential for businesses because it is the most effective way to keep your items in pristine condition. Without it, the possibility of corrosion, moulding, cracking, and other damages increases. Some items that should be stored in a climate-controlled space include furniture, important documents, electronics, and specialist equipment.
2. Place Popular Products or Most-Used Items at the Front

Placing your most popular items or frequently used supplies at the front of your storeroom or steel rack shelving allows your staff to function at full potential because they can quickly grab what they need and return to operations without spending time looking for things. Having to dig for products among a jumble of other items messes up any organised system, and this method of arrangement can help prevent that. This also gives you visibility into your inventory, allowing you to easily track sales trends and determine which items sell the best and need to be replenished as soon as possible.
3. Utilise Inventory Management Techniques and/or Softwares
The key to effective inventory management is to create an arrangement system in which items are placed according to different categories. For instance, by their colour, size, style, or purpose.

Once you've decided how to organise your stock, plan out your warehouse layout to house each item. If you have a large storeroom, it may be helpful to arrange your shelves and goods alphabetically. Additionally, map out different zones and provide a visual guide for employees to use when looking for items. This guide should be updated on a regular basis.
Businesses can use stock control management softwares to keep track of their stock levels, orders, sales, and deliveries. These systems can help to improve productivity by streamlining your company's day-to-day processes and improving communication across departments. With a comprehensive inventory overview, you'll be able to meet your company's supply needs or customer demand in a more efficient and effortless manner.
4. Invest in the Right Storage Units and Accessories

There are multiple kinds of storage units available, including stainless steel shelves, racks, drawers, cabinets, wire security cages, and more, but not all of them will be suitable for your business. The best storage unit or accessory that will work for your business is determined by the type of stock you hold. For example, if you need to frequently transport items around your facility, a mobile shelving solution will be one of the most useful pieces of storage equipment to have because it allows you to maximise your space and move things around.
Before purchasing storage supplies for your company, make sure that your supplier can provide you with high-quality equipment with protection from fire hazards, water damage, and theft. Consider the size of the units and the quantity of equipment you need based on the size, arrangement, and layout of the space you have.
Optimising Your Storage System
2.1. Storage Equipment Must-Haves

Stainless steel racks and shelves are excellent choices if you need to put together a storage facility. Stainless steel equipment is robust and durable, as well as easy to maintain.
1. Stainless Steel Work Tables
Stainless steel work tables are necessary in storage facilities not only to hold small items, but also to serve as an additional sturdy workstation for operational purposes. For example, labelling, holding computers, packing, or stacking small containers of supplies and stationeries.
2. Stainless Steel Garment Rack
Garment racks are designed to hold lab coats, smocks, and other garments used in commercial or medical environments. The majority of garment racks are made of open wire, which allows for smooth airflow to prevent dust buildup and keep garments as sanitary as possible. These may be useful for your facility if you work with hazardous or sensitive substances that require high levels of cleanliness.
3. Steel Rack Shelving
Stainless steel rack shelvings can be equipped with storage accessories such as baskets, shelf dividers, hooks, and more for better organisation, which make them highly versatile equipment. These stainless steel shelves can be used in just about any facility, but are excellent choices for cold storage warehouses, retail organisation, long-term record keeping, and other similar storage applications. Their open wire shelf allows more light to penetrate and air to circulate, improving visibility and cleanliness.
4. Stainless Steel Wire Trolley
Stainless steel wire trolleys are mobile storage solutions that can be used to store items that need to be moved around regularly, such as in medical institutions or packing facilities.
2.2. Maximising Your Storage Space

No matter how well-planned a storage facility is, little pockets of space tend to remain, which is an inefficient use of space. However, utilising every awkward corner or narrow aisle is not that simple because there are numerous factors to consider. Here's how to make the most of your storage space.
1. Smaller Equipment
The first step towards making the most of your small space is to find equipment that fits. For example, corner wire shelves, smaller stainless steel shelf racks, or trolleys that can slide in and out of small spaces easily.
2. Customised Storage Solutions
There are many different storage unit sizes, and not all of them will fit perfectly into your facility. Rather than filling your premises with equipment that does not maximise storage capacity, tailor each piece of equipment to the size of your warehouse so that you do not leave pockets of empty space everywhere. This allows you to personalise your storage solutions based on the size and quantity of your products, as well as make full use of your floor space.
3. Build Vertically
If floor space is limited, building vertically is a great way to expand your storage capacity. The same area used to store 10% of your stock can store up to 20% with additional shelves reaching the ceiling.
2.3. Ensuring Storage Safety
Poor maintenance and misuse of shelving racks in Singapore warehouses have resulted in several workplace injuries and deaths that could have been avoided. Workplace safety is critical in storage facilities because the hazards of falling equipment and/or inventory can be disastrous. Here are some protective measures to take to ensure your facility's safety and prevent fatalities.
1. Remove Potential Hazards
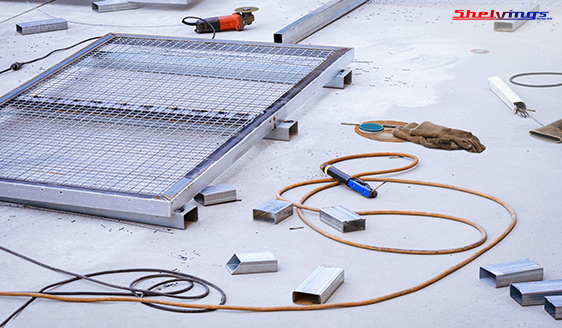
The area surrounding every one of your shelving racks should be kept clean and clear at all times. Even if your employees are extremely cautious, safety hazards such as stray cords, wires, flammable liquid, cracked floors, and spills can all cause accidents.
2. Store According to Manufacturer Instructions
Every storage equipment comes with manufacturer’s instructions outlining its proper usage guidelines and its recommended storage capacity. These should be strictly adhered to in order to avoid overloading or damaging your shelf racks. Stacking too many items on your racks can damage your storage unit and even cause an accident.
3. Follow Safe Processes
Even in the safest facilities, accidents are bound to happen if employees do not follow safe operating procedures. Employees should avoid climbing onto shelves to retrieve items, especially stainless steel shelves that are not secured to the ground as it may collapse or fall over; attempting to grab items from a height without the proper tools can result in them falling onto the worker; running around the facility with or without items on hand can result in tripping, slipping, or falling. Proper training should be conducted to prevent employees from committing such dangerous acts that can endanger their lives.
2.3.1. Chemical Safety

Laboratories that handle chemicals and other similar substances face a variety of risks that can affect either the laboratory's operations or the general public. While some substances are beneficial, others are hazardous to human health and the environment, and some may even be used to create weapons or drugs that endanger the public's security Aside from hazardous chemicals, laboratories contain sensitive information and expensive equipment that must be protected, and chemical safety and security can mitigate these risks.
Essential Equipment for Chemical Safety
Labels

Labels are the most basic item to have in laboratories. They clearly identify each item, what it contains, and provide additional information on the proper storage, use, and disposal of substances, as well as ensuring that other users have access to these information.
Safety Data Sheets
Safety Data Sheets include information regarding each chemical that cannot be properly listed on labels, such as its properties, the potential hazards, protective measures, and the proper handling, storing, and transporting of the chemical.
Appropriate Storage Equipment
Different substances have their own specific safe storage requirements and it is important to use the right type of laboratory storage shelves and equipment to ensure chemical safety and prevent accidents. consider whether any of the chemicals are carcinogenic, mutagenic, or toxic, how they should be stored, where they should be housed, which chemicals cannot be stored next to each other, storage conditions such as temperature, humidity, and ventilation, and proper disposal methods.
Storage of Different Substances
a. Acids: Concentrated acids must be stored in acid-resistant cabinets made of polypropylene, HDPE, or wood, with a tray to catch any spills or leaks. Wooden cabinets should not be used to store oxidising acids. Acid chlorides and fuming acids should be stored in ventilated containers. Acids must be kept separate from alkalis and flammable liquids.
b. Alkalis: Store away from acids
c. Flammable Solvents: These should be kept in specialised cabinets made of metal or wood that have a minimum fire resistance of 30 minutes and a spillage tray to catch leaks and spills. Cabinets should be clearly labelled and placed away from escape routes.
d. Chlorinated Solvents: These must be stored away from flammable solvents and alkali metals, as spillage can cause fires and explosions. Keep them in well-ventilated cabinets.
e. Noxious Chemicals: Store them in ventilated cabinets.
f. Oxidisers: Store them in a metal or other non-organic storage unit, away from other materials such as flammable solvents or reducing agents.
g. Carcinogens and Mutagens: Keep them in a safe and secure cabinet. Only authorised individuals should be granted access to them.
2.3.2. Food Safety

Bacteria can multiply quickly on food items if they are left in dangerous temperature zones of between 5℃ and 60℃, causing food poisoning in the people who consume them. Any mishandling during food preparation or storage can lead to contamination and result in food-borne illnesses. All fresh or frozen food products must be stored in refrigerators or chillers at 4℃ and below, or freezers at -18℃ and below. Any dried and preserved food items should be stored in a cool and dry place, or kept in a chiller to prevent them from going bad. Other important food storage guidelines include:
Cool hot food entirely before storing them in the refrigerator
Avoid refreezing thawed food as bacteria can grow while it is thawing
Always thaw frozen food in the refrigerator and not in open air
Raw food and cooked food should be stored separately as cross-contamination can happen
Raw food should be stored in sealed or covered containers at the bottom of the refrigerator
Use only strong, non-toxic food-safe containers
2.3.3. Cleanroom Safety
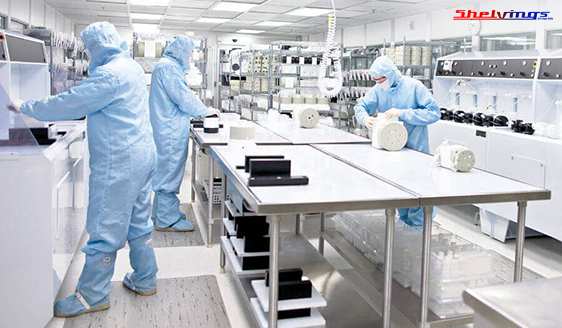
Cleanrooms are highly controlled environments with air quality, temperature, and humidity strictly regulated for the safe handling of sensitive items such as electronic equipment, pharmaceuticals, medical devices, or product manufacturing. Aside from climate control, there are numerous other important rules to follow in order to keep cleanrooms clean.
1. Practise Good Hygiene
Employees must maintain good personal hygiene and keep their work environment clean at all times. To keep the cleanroom sanitary, all employees should thoroughly wash their hands, clean away any dirt on them, and put on the appropriate protective equipment before entering the cleanroom. Equipment, supplies, and tools used must also be cleaned before and after use.
2. Follow Proper Procedures
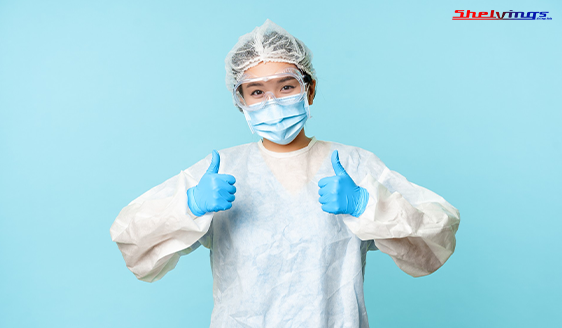
To avoid cross contamination in the cleanroom, employees must be trained and expected to work within the safety guidelines that have been established. For example, the proper ways to put on and remove any cleanroom garments, the correct method to clean surfaces and supplies, as well as procedures to adhere to before and after entering or exiting the cleanroom. There are even steps to follow in cleaning and maintaining the cleanroom. Each class of cleanroom has its own suitable cleaning equipment and solvents, and employees must ensure that they are using the appropriate tools before beginning any cleaning task. Some of them include lint-free materials, non-shedding wipes, stainless steel buckets, and HEPA filter vacuums.
3. Cleanroom-Designated Supplies
All cleanroom equipment and tools should be kept in the facility and never removed, as bringing them in and out can cause contamination. Always use cleanroom-designated supplies and never bring outside supplies into the cleanroom.
Additionally, there are storage equipment designed specifically for use in such controlled environments. For example, perforated stainless steel tables. They go through an electropolishing finishing process that removes a thin layer of material from the metal part, leaving behind a shiny, smooth, and ultra-clean surface that reduces particle retention and keeps surfaces clean.
Perforated stainless steel tables have uniformed holes across the table surface, allowing laminar airflow to flow directly through the work surface, encircling everything with clean and fresh air and carrying away any airborne contaminants. As a result, they contribute to keeping the workstation clean at all times.
2.3.4. Maintaining Cleanliness
Stainless steels are the preferred material choice in any commercial facility because they are durable and easy to maintain. However, no matter how strong they are, damages and corrosion can still happen if they are not maintained properly. Rust may not be harmful to human health, but it can significantly weaken and damage metals such as stainless steel shelving racks. Singapore has high humidity levels, the excess moisture in the air can quicken the corrosion process. But with the right methods, you can easily protect and maintain your stainless steel equipment. Here’s what you need to do.
1. Keep them Dry
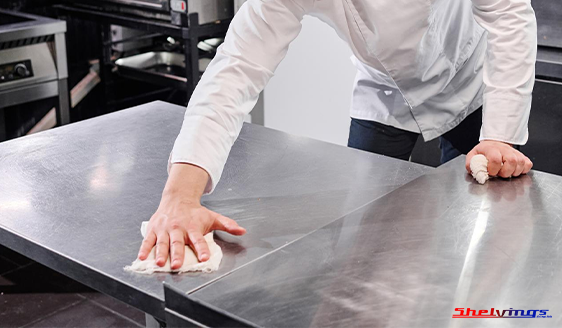
Do not allow moisture to sit on any metal surfaces because the oxygen particles in water molecules will cause rust to form when they come in contact with the iron content in metals. To keep your stainless steel racks dry and clean, simply use a soft cloth, warm water, and mild detergent to wipe down surfaces. Then, thoroughly wipe them dry. Additionally, you can invest in a dehumidifier to lower humidity levels and reduce the risk of corrosion.
2. Apply Protective Coat
Protective coatings, such as lubricants, sprays, and paint, are excellent for preventing scratches and corrosion. There are numerous coatings available, each of which can be used to protect your equipment from a specific type of damage. For example, anti-corrosion paints.
3. Avoid Using Abrasive Materials
Scratches or cracks appear on stainless steel when abrasive cleaning tools such as steel wool, harsh chemicals such as bleach, and other similar items are used. This exposes the metal's iron parts to more moisture and oxygen, resulting in corrosion. Some cleaning tools contain iron and can leave iron deposits on the metal, reducing its corrosion resistance over time. Therefore, it is advised to avoid using such materials.
If you must store chemicals on your stainless steel shelves, keep them tightly closed in appropriate containers and keep a spillage tray near each one to keep the chemical from coming into contact with your stainless steel.
Proper storage and inventory management entails more than just storing, handling, and disposing of stock and supplies in your warehouse. From the selection of stainless steel racks for storage to the maintenance of every piece of equipment in your facility, every phase of your operation is critical to effective organisation. Be sure to do ample planning prior to making your purchase to ensure safe operations and orderly storage.
Shelvings is a leading manufacturer of quality, durable, and heavy-duty stainless steel shelf racks in Singapore. From design to installation, we offer a variety of storage solutions customised to your business needs. Find the perfect shelving solution with us.
Comments